MAINTAINING FINANCIAL ACCOUNTABILITY In the ship's store operation, each custodian must maintain financial accountability for all stock within his or her area of responsibility. This simply means that the custodian is responsible for maintaining the money value of all stock to prevent a shortage or overage during inventory. Past inspections have shown that the single most contributing factor to lack of financial accountability for stock in the bulk storeroom is a breakdown in internal checks and controls. Although human perfection is virtually impossi-ble, the custodian of the bulk storeroom must always strive to come as close to perfection as possible. The internal checks and controls we are talking about are included throughout the Ships Store Afloat, NAVSUP P-487, and are designed to cut down or eliminate inventory shortages. In this section we discuss some of the major checks and controls considered necessary in maintaining financial accountability in the bulk storeroom, but it will be entirely up to each individual bulk storeroom custodian to always follow the correct procedures outlined in the NAVSUP P-487 when performing daily tasks. Errors in Receiving When the bulk storeroom custodian acknowl-edges receipt of ship's store stock, he or she is accepting responsibility for the disposition of that stock. However, if the responsible custodian does not follow the correct procedures for receiving stock, then he or she is risking financial accountability of the bulk storeroom. All material received is inspected by the ship's store officer or designated receipt inspector for quantity, quality, and damage. Once this is done, the material is carried to the bulk storeroom. The bulk storeroom custodian will obtain the retained receipt documents from the Incoming Material File (SSA-20), take them to the bulk storeroom, and wait until the stock is brought by the working party. The responsible custodian will make sure boxes brought to the storeroom are not opened and all boxes arrive. If boxes are being numbered by the receipt inspector, the custodian will make sure all numbers are accounted for. Only person-nel authorized by the bulk storeroom custodian should be in the storeroom to assist in loading operations. The custodian of the bulk storeroom accepts the merchandise by circling the quantity received on the receipt document and signing the accountability stamp as shown in figure 3-2. If the quantity of the item counted is not the same as what is shown on the receipt document, record and circle the actual quantity received and cross out the quantity shown on the receipt document. All cross outs must be initialed. The custodian accepting the merchandise and signing the accountability copy is legally responsible for the proper disposition of the material while it is in his or her custody. The custodian will forward the copy of the signed receipt document to the ship's store officer. The custodian receiving stock into the bulk storeroom must make sure what is signed for is exactly what is received. The custodian must never take for granted what stock is received and just sign the stamped receipt document. The custodian must always make sure the quantity received is the same as shown on the receipt document. If it isn't, the custodian must change the quantity shown on the receipt document to the actual amount received and circle it. It is acceptable for the custodian to use the quantity indicated on the outside of the container if the container has not been opened previously. If the container has been opened before, do not take for granted all the merchandise is in the container- always check it carefully. Movement of Stock Most stock movements between the bulk storeroom, sales outlet, and service activities are accomplished through breakouts, breakbacks, and intrastore transfers. This includes items that will be sold to customers and items to be consumed directly in the performance of service for customers such as the laundry or barbershop. Items that are carried for sale in the sales outlet are considered retail items. Retail items include items sold through the retail store, the snack bar, vending machines, and standard Navy clothing sold at standard prices. The internal movement of these retail items is commonly referred to as a breakout.
Figure 3-2.- The bulk storeroom custodian accepting receipts. Items that are carried for ultimate expenditure as cost of operation materials and cost of sales items are called cost items. Cost of operation items include items used in the performance of service to customers; for instance, items used in the laundry, barbershop, and repair parts used for the vending machines and snack bars. The internal movement of cost of operation items is referred to as an issue. Cost of sales items require further processing or manufacturing and include snack bar ingre-dients, soft drink syrup, carbon dioxide gas (CO2), straws, spoons, and paper cups. The internal movement of cost of sales items is referred to as a breakout, like retail items. A breakback is just the opposite of a breakout. The breakout is when merchandise is transferred from the bulk storeroom to the sales outlet while a breakback is when merchandise is taken from the sales outlet and returned to the bulk store-room. The internal movement of stock whether breakout, breakback, or issue is documented on an Intra-Store Transfer Data, NAVSUP Form 973. Requests for breakouts are routed by the sales outlet or service activity operators to the ship's store office for processing. After the office prepares a NAVSUP Form 973, there are certain procedures the bulk storeroom custodian should follow. The ship's store office will distribute the original and duplicate copy of the NAVSUP Form 973 to the bulk storeroom custodian to issue the stock. The triplicate copy is retained by the records keeper. The quadruplicate copy is given to the sales outlet or service activity operator receiving the stock. On receipt of the original and duplicate copy of the NAVSUP Form 973, the bulk storeroom custodian will break out the stock. The bulk storeroom custodian must record the quantities broken out on the two documents and sign and forward the original to the office recordskeeper. The duplicate copy is retained by the bulk storeroom custodian. The sales outlet or service activity operator will not have access to the original or the duplicate copy. Once the stock is received in the sales outlet or the service activity, the operator will record the quantities received on the quadruplicate copy of the NAVSUP Form 973. The operator acknowl-edges receipt of the stock by signing the quadruplicate copy and forwards it directly to the recordskeeper. After the recordskeeper receives the original and quadruplicate copy, the quantities received will be circled on the original and entered and circled on the triplicate copy. If a discrepancy is noted between what the bulk storeroom custodian broke out and what the sales outlet or service activity operator received, an inventory will be conducted immediately of the item in the bulk storeroom and the count compared against the corresponding Stock Record, NAVSUP Form 464. After reaching an agreement on the actual quantities broken out, the bulk storeroom custodian and sales outlet operator will correct and initial all copies of the NAVSUP Form 973.
|
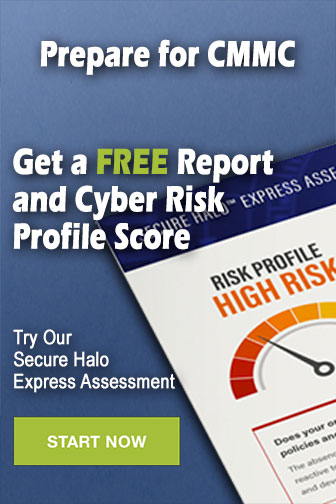
|