HYDRAULIC
GOVERNORS.-For its speed-sensitive elements, the hydraulic governor, as
shown in figure 9-27, depends on a similar flyweight arrangement to that of the
mechanical governor. However, the power supply that moves the fuel mechanism is
operated hydraulically rather than through direct mechanical linkage with the
flyweights. The flyweights of the hydraulic governor are linked directly to a
small pilot valve that opens and closes ported passages, admitting oil under
pressure to either side of a power piston that is linked to the fuel control
mechanism. Since the flyweights move only a lightweight pilot valve, the
inherent design of the hydraulic governor is more sensitive to small speed changes
than the design of the mechanical type of governor, which derives all of its
working power from the flyweights. The larger and heavier the fuel control
mechanism, the more important it is to employ a hydraulic governor. There
is always a lag between a change in fuel setting and the time the engine
reaches the new desired speed. Even when the fuel controls are set as required
during a speed change, hunting caused by overshooting will occur. As long as
engine speed is above or below the desired new speed, the simple hydraulic
governor will continuously adjust (overcorrect) the fuel setting to decrease or
increase the delivery of fuel. For this reason, a hydraulic governor must have
a mechanism that will discontinue changing the fuel control setting slightly
before the new setting has actually been reached. This mechanism, used in all
modern hydraulic governors, is called a COMPENSATING DEVICE.
One
type of compensating device is illustrated in figure 9-27. The buffer piston,
buffer springs, and needle valve in the hydraulic circuit between the control
land of the pilot valve plunger and the power piston comprise the BUFFER
COMPEN-SATING SYSTEM of the governor. Lowering the pilot valve plunger permits
a flow of pressurized oil into the buffer cylinder and power cylinder. This
flow of oil moves the power piston up to increase fuel. As the pilot valve
plunger moves up, oil is permitted to flow from the buffer cylinder and power
cylinder to the governor sump, and the power piston spring moves the power
piston down to decrease fuel. The rate of compensation is adjusted by
regulating the oil leakage through the compensating needle valve. If the
compensating needle valve is adjusted correctly, only a slight amount of
hunting will occur after a load change. This hunting will quickly be dampened
out, resulting in stable operation through the operating range of the governor.
|
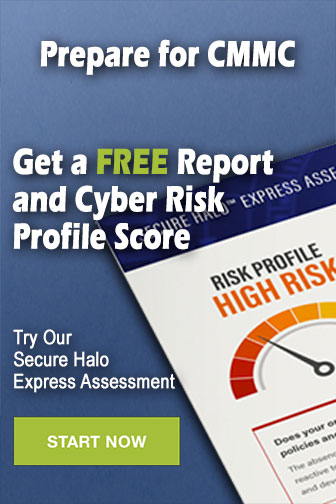
|