SERVICING THE VENDING MACHINES The operation of the vending machines is sometimes referred to as automatic merchandising. However, the only thing automatic about it is the customer drops a coin into the machine and receives the product in return. Everything else is done by the vending machine operator who services the vending machine. Filling the Vending Machine Filling the vending machine (fig. 2-14) is much easier if the product is stored properly before being dispensed. For instance, during the process of shipping and handling of soda cases, there may be the possibility of damage occurring that goes unnoticed. If these damaged cases are not removed, the cardboard, plastic wrap, and cans in the cases below or adjacent to the damaged cases often remain wet for long periods of time.
Figure 2-14.-Filling the vending machines. To prevent this damage, leaking or wet cases must be identified and removed from the pallet. We will discuss damaged cases and storage of different stock items later in chapter 3 of this TRAMAN. Before you fill the machine, go to each individual machine and count how many of each flavor you will need to fill the machine. Do not guess at how much merchandise you will need or you may find yourself carrying merchandise back to the storage area. Make sure everything you bring to the vending machine is clean and free of damage. Open the machine and place the merchandise in its correct slot or space in the machine. Nothing is more disturbing to a customer than pushing for their favorite brand and receiving something else. Not only will the customer get the wrong product but the vending machine operator is not always readily available to assist the customer. It is best to place a sign on the machine with your name, rate, and ship's telephone number where you can be located if any problems occur. When restocking canned soda machines, do not forget to indicate on the daily record of vending machine drinks how many sodas you have placed in the machine by flavor, if this is required. After you have filled all slots in the machine, test the vending machine for proper operation. It is very disturbing to the customer when the vending machine will not operate or will not accept money. Cleaning the coin changer regularly will help to prevent contact surfaces from becoming sticky and jamming coins. Make sure all machine lights are in proper working order such as sold-out lights and correct change lights. If you do not replace these burned-out lights and they are inoperative, the customer will put the money in thinking the product is in the machine when it actually is not. They will probably then have to settle for a product they did not want. If you leave the correct change light inoperative, the customers may put incorrect change in thinking they will get their change back and they will not because there will be no change in the machine. Also place a sign on the machine stating the time it was last filled so the customer will know how cold the sodas might be. It is best to fill the machines about an hour before work starts so the sodas in the machine are cold by the time the workday starts. When possible, you should always try to fill the machine with brand name products. Do not fill the machine with off-brand products that do not sell. You might not have to fill the vending machine as often; however, you are doing your shipmates an injustice and not doing your job according to the purpose of the ship's store. Remember, when you stick to name brand products you cannot go wrong. The most important factor for you to remember when filling the machines is the timely scheduling of refilling the vending machines to make sure there is a continuous supply of products and services. Not scheduling your refilling times properly will result in empty machines or columns and unsatisfied customers. Remember, you may have to adjust your schedule for specific weather conditions. You sell more sodas when it is hot than when it is cold. On paydays, machines have a tendency to empty more quickly. As you gain experience in filling the machines, you will learn to adjust to these specific conditions. Vending Machine Displays All product displays should be kept neat and clean and look appealing to the customer. Displays should be changed frequently to stimulate customer interest. Light bulbs for displays should be changed as soon as they burn out. Broken or discolored glass should be replaced as soon as possible. Plastic product decals are normally available from the company you purchase sodas from and should be used. Never use handwritten signs, if possible.
|
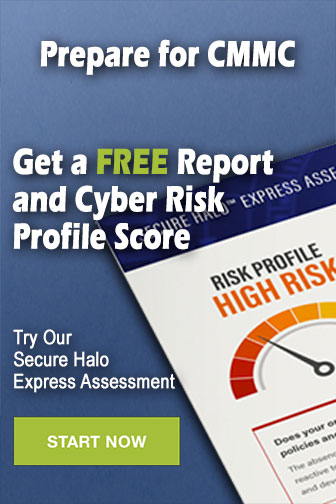
|