DISPOSAL AND ENVIRONMENTAL PROTECTION The Environmental Protection Manual, OP-NAVINST 5090.1, issues Navy policy and assigns responsibilities for Navywide actions for control of environmental protection. Commanding officers should coordinate and cooperate with
federal, state, interstate, and local pollution control agencies, and follow all standards and regulations in regard to control of environmental pollution. As a Ship's Serviceman, you should be aware of practices or things that may affect the environment. The water that drains from the
laundry is considered waste water and is transported to the collection, holding, and transfer
(CHT) tanks. CHT tanks are installed aboard ship for the purpose of handling waste water from showers, heads, laundries, galleys, sculleries, and sinks and is transported by the ship's waste drain system. In port the waste water is transferred ashore for disposal. Underway, the ship should not be within 50 miles of any shoreline to discharge this waste. Before you dispose of any laundry chemicals
in port or at sea, you should first consider whether it is a hazardous substance. A hazardous sub-stance may be defined as any substance or mixture of substances that is toxic, corrosive, irritating, flammable, a strong oxidizer, a strong sanitizer, or that generates pressure through decomposition, heat, or other means. Hazard classifications and stowage requirements for shipboard consum-ables
are contained in NAVSUP Publication 4500, Consolidated Hazardous Item List (CHIL), now known as the Hazardous Materials Infor-mation
System (HMIS) list. Information on the disposal of hazardous substance is included in
sec-tion A of this publication. Section A includes a disposal code for each item listed and explains
pro-cedures for disposal of that particular substance. LAUNDRY SCHEDULES The laundry supervisor prepares the laundry schedule for approval by his or her immediate
supervisor. As a Ship's Serviceman third class, you should be familiar with factors that determine not only the laundry schedule but how many hours the laundry will be operating. These factors include the following: . Amount of work that must be processed weekly . Capacity of laundry equipment . Number and competence of laundry crew These factors listed may be overwhelming at times. To eliminate problems and establish normal working hours for personnel, a laundry is generally operated in shifts. A laundry shift normally lasts 8 hours. Your laundry may operate one, two, or three shifts per day. Each shift must have experienced Ship's Servicemen to handle each shift so work turned out is satisfactory. A shortage of experienced personnel will require strikers to assist SH personnel. Strikers should not be allowed to operate equipment until they are qualified in using that equipment. PROCESSING LAUNDRY The first step to processing laundry is receiving the different lots into the laundry, marking them, and classifying them. Articles to be laundered are delivered to the ship's laundry either in bulk lots or in individual bundles. Bulk lots include division laundry (crews' personal clothing and linen), flatwork (towels, linen, and tablecloths from staterooms, officer and CPO messes, and sick bay), and service lots (clothing of cooks and foodservice attendants, barbers, hospital
per-sonnel, and snack bar personnel). The workflow for individual and bulk lots is shown in figure 5-6.
The solid black line running from the Bulk Lots block, top left, to the Issuing block at the bottom shows the steps in processing bulk laundry. The broken line on the right side of the chart connects all types of work accomplished on individual lots. The receiving laundry personnel are
re-sponsible for receiving, marking, and classifying all lots delivered to the laundry. To perform these duties, the receiver should
have a list of divisional laundry petty officers. The laundry supervisor provides the receiver with this list in case there is a need to contact a division representative regarding delivery and pickup of laundry or to resolve problems. Meetings are normally held periodically by the laundry supervisor to inform divisional laundry petty officers of any changes that may occur in laundry policy. RECEIVING BULK LOTS When receiving bulk lots, the receiving laundry personnel should consider the many problems that may be encountered when identifying, classifying,
and marking these bulk lots. Bulk lots are delivered to the laundry in large divisional laundry bags. You should be careful not to accept laundry bags that are overstuffed. Overstuffed laundry bags cause handling problems during the laundry process. For the purpose of safety and production standards, divisional laundry bags should not be accepted over your washer extractor capacity. If you do accept bags over your capacity, they will have to be split upon the wash deck causing delays
and possible claims for loss of clothing. Check bulk lots and make sure the division name is stenciled in large letters on all divisional laundry bags received. You should also check bags to make sure blues and whites are not mixed in one bag. If a divisional laundry bag makes it past the receiving section mixed with blues and whites, it will delay the laundry process on the wash deck as the divisional laundry in the bag will have to be separated. Divisional bulk laundry bags should not be accepted until all discrepancies noted above have been corrected. If policies concerning your laundry process are given to divisional laundry petty officers during the monthly meeting, problems will be eliminated. RECEIVING INDIVIDUAL LOTS Bundles received daily in the laundry from officers and chief petty officers are considered as one lot of individually marked bundles. If you have more bundles in the daily lots than available
assembly bins, it is best to set up two lots daily. You can then assemble and check out the bundles in the first lot before work from the second lot
comes to the assembly bins. Twenty bundles in a lot are easy to handle. Never put more than 50 bundles in one lot. The number of bundles you should put in a lot is affected by the classification of the items in the bundles. Classification is the separation of a bundle of laundry according to color, type of fabric, and degree of soil; that is, white cottons,
Figure 5-6.- Workflow for a laundry operation. other white or light-colored fabrics, light cottons with heavy stains, dark-colored cottons, and so forth. Items are classified according to the washing formulas to be used.
|
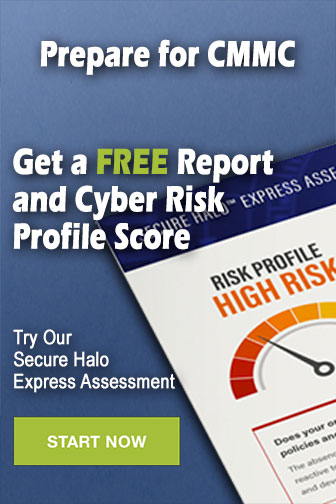
|