Accessibility of Stock Accessibility of stock is simply allowing yourself the capability to reach and remove any stock items out of the bulk storeroom with the minimum of effort. Accessibility of stock is a very important fundamental of good stowage. When you receive new stock you must keep in mind that some day you will issue or inventory items in the storeroom. You do not want to stock 20 cases of an item on 1 case of a different item. More than likely you will use that 1 case before you use the 20 cases. With proper arrangement and use of the storeroom facilities you should never have this problem. Arrangement of Stock Bulk storerooms should be neat and orderly and, when possible, container labels should be facing out. Containers should be arranged by item, brand name, and date of receipt or date of manufacture. This way the contents of the item can be determined without handling each item and it will facilitate breakouts, inventory, and proper turnover of stock. Case lots should be stowed on deck gratings and not placed directly on the deck. A few things to keep in mind when you are arranging stock are discussed below: Item similarity- Items that are similar and have similar handling requirements should be stowed together when practical. This will make your job of issuing and controlling these stock items easier. Item popularity- The popularity of an item must also be considered when arranging stock. Fast-moving stock should be stowed in areas that are easily accessible. Slow-moving stock should be stowed away from easily accessible areas. Item size and weight- The size and weight of the item not only affect the amount of stowage space needed, but also affect your decision on where you will stow it. For example, a large, heavy item should be stowed in a location that will provide a balance between accessibility and required handling. In other words, do not stow heavy laundry supplies in the forward portion of the ship while the laundry is located aft. Item quantity- The quantity of the items to be stocked affects the amount of space required and will affect the arrangements of other stock. If you have a large number of one stock item, it is always better for you to increase the amount of space needed to stock all the items in one space than splitting the items up into two or more different locations. Keeping the item in one location will also help in accounting for the item especially during inventory. Breakable material- Fragile material should never be stowed in the same location with heavy material. It should be stowed in a separate location to prevent excessive movement while the ship is underway. Empty cardboard cartons may be cut into strips and used to fill unused space where fragile material is located. Material received in glass containers must receive special attention since breakage not only results in loss of the item but may cause damage to other stores or create a hazard to personnel. Aisles- When arranging stock, position an aisle about 30 inches wide in the storeroom so you will have access to all stock. If an aisle is not maintained, you will have to remove several items to get to others during breakouts or issues and inventory can turn into a nightmare. It is generally recognized that just before deployment and 1 month into deployment it may be hard to main-tain an aisle in the storeroom due to the amounts of stock on board. Lack of stowage space is a very evident problem aboard ship and during pre-deployment planning these problems need to be resolved. The supply officer may be able to negotiate with other department heads for additional stowage space. If additional space is not available, stowage plans will have to be made on the space available. Item characteristics- Most items of ship's store stock are of such nature that special stowage is not required. However, there are some stock items that require special considerations such as flammable stock, perishable stock, and so forth. We discuss some of these stock items later in this chapter. Storeroom Maintenance The responsible custodian of the bulk store-room is responsible for cleaning and maintaining the space, including keeping the storeroom free of items that should be surveyed because they are damaged or deteriorated. When such items are present in the bulk storeroom, the responsible custodian should notify his or her supervisor so action can be taken to mark them down or survey them. The neatness, cleanliness, and order of the bulk storeroom are also responsibilities of the custodian. These are carried out by proper housekeeping and maintenance of the space. Observation of good housekeeping practices in the bulk storeroom promotes safety, reduces losses from damage of merchandise, reduces fire hazards, and increases the efficiency of the bulk storeroom operation. Before you secure for the day, break down all loose boxes, sweep, and remove all trash from the bulk storeroom. Also inspect and clean bins, shelves, ventilation ducts, and fans periodically. After major receipts or breakouts, stock should be organized with the content labels visible. The material condition of the space is also the responsibility of the responsible custodian. For instance, rust is an ever-present enemy and requires constant vigilance to keep it under control. Rust spots should be chipped, brushed or sanded, primed, and spot painted. Loose bolts should be tightened promptly to prevent possible damage to the storeroom or its contents. Pipes, valves, electrical systems, watertight fittings, and fire-fighting equipment must be examined daily and any defect reported to the ship's store officer. The ship's store officer should inspect all ship's store activities under his or her control each business day and submit required reports to the supply officer or duty supply officer before 8 o'clock reports. The method and the time of these reports are established in each ship's routine. Before getting underway into open seas, storerooms must be thoroughly inspected and secured to prevent stores from shifting due to the ship's motion. Bulk stores must be braced or lashed to bulkheads, stanchions, or battens, and the fronts of open bins and shelves secured to prevent stores from falling out on the deck. Once you check and prepare your storerooms for sea, notify your supervisor to have the storeroom checked. After all ship's store spaces have been prepared for sea and checked, the leading Ship's Serviceman reports to the ship's store officer that all ship's store spaces are ready for sea. The ship's store officer passes this information to the supply officer so readiness reports for getting underway may be given to the officer of the deck in the pilothouse. Issue and Rotation Earlier you learned that the oldest stock on hand in the bulk storeroom should be issued first. Generally speaking, it is first in and first out. However, when deployed overseas, you may receive stock from naval supply depots or combat logistics force (CLF) units that was manufactured before the stock procured in the United States when loading out. Manufacture age codes that we discussed earlier are especially important in this case because they indicate the date of manufacture. In the instance above, the new stock just received is actually older than the stock already in the bulk storeroom and should be issued first. Ventilation and Humidity Control All storerooms must be well ventilated to prevent excessive heat and humidity because high temperature and humidity encourage bacteria growth and insect infestation. In addition, high humidity can result in mold and mildew and may cause mustiness in cookies, crackers, and tobacco products. Of course you have no control over storeroom location, but you are responsible for making sure space is left between cases and structural obstructions such as steam pipes to permit maximum ventilation. When possible, bulk storerooms will be ventilated once a week to permit air circulation and to remove stagnant air that can cause damage to perishable items.
|
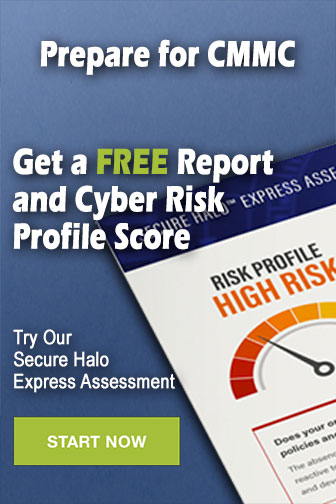
|